Different types of POP displays are built in different ways. To choose the one that will work best for you, some of the things you’ll have to consider include: your budget, how long you need the display in your store, where you plan to use it within your store, and what products you want to have in the display.
- Wire Canister Brackets
- Free Standing Display Units (FSDU)
- Shelf Edging
- Standees
- Counter Display Units
- Endcaps
- Display Stands
- Floor Displays
- Plastic Extrusion Displays
- Semi-Permanent Displays
- Permanent Displays
- Temporary Displays
- Sheet Metal
- Wire Forming/Bending
- Custom Plastic Thermoforming
- Injection Molding
Sheet metal is an ideal material for POP (Point of Purchase) display stands due to its strength, durability, and stability. It can support various products without bending or toppling over, making it reliable and safe in a retail setting. Sheet metal is customizable, cost-effective, and versatile, offering businesses the ability to create visually appealing displays that can be tailored to specific design needs. Its easy maintenance, recyclability, and long lifespan also make it a sustainable choice for display stands, though it's essential to consider factors like weight and transportation when opting for sheet metal as the material of choice.
Wire forming and bending techniques are integral to the design of point-of-purchase (POP) displays, offering versatile solutions to enhance the visual appeal and functionality of these marketing tools. Wire components play various roles, such as providing structural support, creating hooks and hangers for products or promotional materials, forming shelving and baskets for better product presentation, and serving as sign holders for conveying essential information. Additionally, wire bending can be used to introduce decorative elements or customized branding into the display, making it more visually appealing and adaptable to specific retail requirements. Ultimately, wire forming and bending help create eye-catching and efficient POP displays that maximize product visibility and customer engagement at the point of purchase.
Custom plastic thermoforming is an essential manufacturing process in the creation of point-of-purchase (POP) displays. Thermoforming enables the production of customized plastic components used in various ways within these displays. It can produce trays, blisters, shelves, platforms, enclosures, faceplates, and graphic overlays, each serving specific functions. Thermoformed components hold, organize, and protect products, create appealing product showcases, and incorporate branding and interactive elements. The flexibility of thermoforming allows for custom shapes, material choices, and color options, making it a versatile tool for designing attractive and functional POP displays tailored to the specific products and branding requirements of a campaign.
Injection molding is a crucial manufacturing process in the creation of point-of-purchase (POP) displays, offering versatility in producing a range of components. It is used to manufacture structural elements, custom plastic parts, shelf brackets, signage holders, product trays, and custom shapes within the display. These components provide support, organization, and branding features, enhancing the overall functionality and visual appeal of POP displays. Injection molding also allows for various color options to match the desired aesthetics and branding. This process plays a significant role in designing attractive and effective displays that capture customer attention and promote products at the point of purchase.
What are POP Displays?
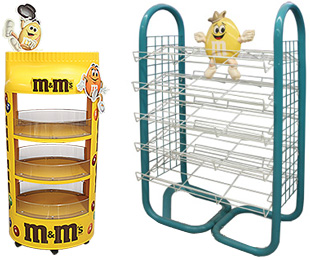
POP displays, also known as Point-of-Purchase displays, are marketing materials or fixtures used by retailers and manufacturers to attract the attention of customers and promote specific products or brands at the point of purchase, typically within a store or retail environment. These displays are strategically placed near the checkout counter, aisles, or other high-traffic areas to encourage impulse buying and enhance the overall shopping experience.
What Type of POP Display Do I Need?
POP displays can take various forms and serve different purposes, including:
-
Standees: These are standalone cardboard or foamboard displays featuring product images, information, and branding. They are often placed at the end of aisles to draw shoppers' attention.
-
Counter Displays: These smaller displays are designed to sit on countertops or checkout registers and usually hold smaller items like candies, magazines, or cosmetics.
-
Shelf Talkers: These are small signs or tags that are attached to shelves to provide additional product information or highlight promotions.
-
Floor Displays: Larger freestanding displays that can hold multiple products, such as stacked boxes of snacks or beverages. They are often used in the middle of aisles to create special product sections.
-
Dump Bins: These are large containers typically filled with discounted or promotional items. Shoppers can sift through the items, making them popular for clearance or seasonal merchandise.
-
Hanging Displays: Suspended from the ceiling, these displays can feature banners, signs, or product samples to capture shoppers' attention from above.
-
Interactive Displays: With advancements in technology, some POP displays now incorporate touchscreens, QR codes, or other interactive elements to engage customers and provide product information.
-
Window Displays: While not typically found inside the store, window displays are a type of POP display used to attract passersby and encourage them to enter the store.
POP displays serve several purposes:
-
Promotion: They help promote specific products, discounts, or special offers, increasing the chances of impulse purchases.
-
Brand Awareness: POP displays reinforce brand identity and help consumers associate certain products with particular brands.
-
Information: They provide shoppers with essential information about products, such as features, benefits, and pricing.
-
Enhanced Shopping Experience: Well-designed POP displays can make the shopping experience more enjoyable and visually appealing.